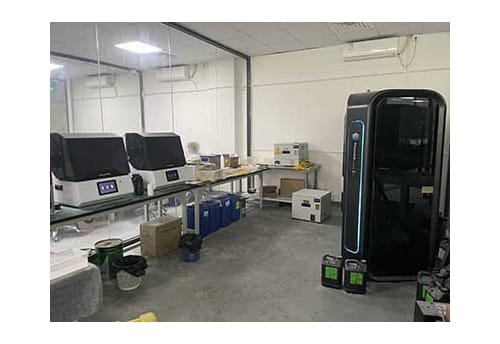
5.Is manufacturing high value-added implant products the future development trend of metal 3D printing technology in dentistry?
In the long term, 3D printing of planting products is an inevitable trend. At present, metal 3D printing technology mainly manufactures dental crowns required for post-implant restoration. The implants and abutments used on the market are standard products, but in many cases doctors need to use personalized abutments for post-repair. At present, the processing technology of abutments is CNC machine tools. The cutting technology of machine tools has high precision, but the processing time is long and the material is wasted. Whether in terms of equipment cost, material saving or processing time, metal 3D printing has application value in the field of personalized abutment processing, but it needs to be coordinated with the development of finishing technology to improve product accuracy.
Domestic implant companies are already developing 3D printed implants. However, in addition to the technical aspects, implant products also involve complex medical device registration processes, and the development cycle of such products is long. If domestic companies can establish and improve 3D printing implant technology and medical certification processes, it may reverse the situation in which European, American and Korean implant brands dominate in the future.
6.How do you view the declining profits of metal 3D printing companies in the field of denture processing?
Unlike other industrial fields where metal 3D printing equipment is used to manufacture high value-added products, the current application of 3D printing of porcelain dental crowns has become a basic processing method in this field. Although there have been improvements in product performance and biocompatibility, the essence of porcelain dental products cannot be changed. In the long term, the application of metal 3D printing technology should focus on higher value-added products, such as not only pure titanium stents, but also implants and personalized abutments.
7.The risk assessment required for international medical certification involves many material science issues (such as material toxicity testing). What related work have domestic 3D printing material companies carried out?
International medical regulatory agencies, such as the FDA, in addition to requirements for the biocompatibility of materials, are also increasingly demanding risk assessments such as chronic toxicity of materials. The cost for material companies to conduct risk assessments is also high, but it is still An area worthy of attention by medical and dental 3D printing material companies.
Cytotoxicity tests are also required during research and development of dental metal 3D printing powder materials. With the development of dental applications, long-term chronic toxicity test data will gradually improve. From the perspective of the chemical composition of the material itself, there is no essential difference between metal 3D printing powder materials and denture processing materials used in traditional processes. It is just that the processing technology is different. The powder materials introduced to the market are within the scope of quality certification standards.
Finished.